![]() |
|
Biography
Ayoub Lahlalia obtained his M.Sc. degree in microsensors and detection systems from Aix-Marseille university, Marseille. France, in 2016. He joined the Institute for Microelectronics, TU Wien, in March 2017 as a research project assistant. His scientific interest focuses on gas sensors simulation, characterization, and data processing.
Enhanced Sensing Performance of Integrated SMO Gas Sensor Devices
Semiconducting metal oxide (SMO) gas sensors are the most investigated type of sensor in the gas sensor family. They can be used in many applications thanks to several outstanding features, namely fast response time, high sensitivity, low fabrication cost and small footprint. These features fulfill almost all the key specifications of a gas sensor with regards to portable device integration. Nevertheless, the poor selectivity, high power consumption and temporal drift of the sensitive layer response and microheater resistance are still hampering full practical integration. One of the key components of this sensor is the microheater. It defines several aspects of the sensor's performance, such as power consumption, sensitivity and selectivity. To enhance the temperature uniformity over the active area and to minimize the power consumption, while making the sensor compatible with application-specific integrated circuit features, a novel microheater structure, a so-called composite heater (see Fig. 1), fabricated on a porous suspended membrane - in order to minimize the thermal mass, as well as the thermal leakage from the heated area to the substrate - is adopted.
To improve the sensitivity and selectivity of SMO gas sensors, the heated area of the sensitive layer must be increased and the temperature must be uniform, since the chemical reactions involved are directly related to the amount of heated surface area in contact with the environment. Due to the high-temperature requirement, however, a large heated area means a larger heater and increased power dissipation. Power consumption depends on microheater resistance, giving rise to a compromise between a large heated area and a small resistance to reduce the power. The novel composite heater design allows for heating a large surface at a uniform temperature while having a small resistance and is created by etching the tantalum-aluminium in different locations (see Fig. 2), which results in reduced power consumption. In addition, a small heater enables a very fast thermal response time, allowing the sensor to operate in short-pulsing mode and with a fast response time. Via this novel microheater structure, heater resistance is reduced, while the heated area is considerably increased, which improves the sensing performance of the device without a significant increase in power.
Fig. 3b shows the temperature distribution over the composite heater design, where a high uniformity in temperature distribution over the active region can be observed. This is a significant improvement as compared to the initial design, depicted in Fig. 3a. The improved uniformity in temperature has been achieved in the composite heater design thanks to the high thermal conductivity of the AlCu conductive pads and the SiN membrane and insulating layer. The heating process is no longer activated by the microheater alone, but also by the AlCu and SiN. Therefore, even though the total resistance is reduced, an overall larger active sensing area is achieved by separating the heating locations.
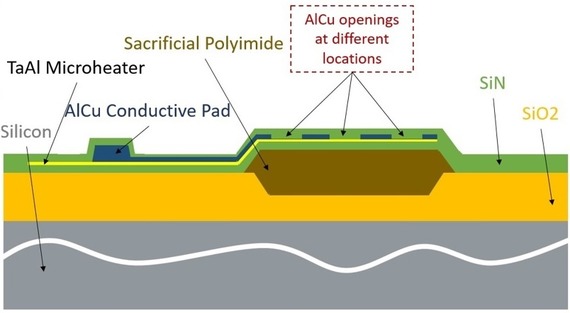
Fig. 1: Cross-section of the novel composite heater design with the AlCu openings. To form the gas sensor membrane, the sacrificial polyimide was etched as the last step in the fabrication sequence using selective plasma etching in order to achieve low power consumption and good thermal isolation.
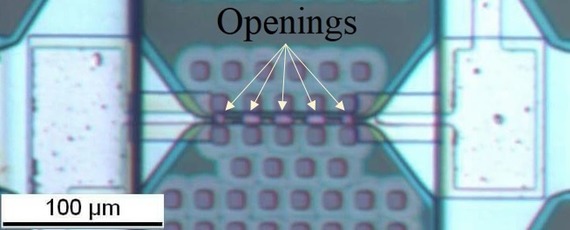
Fig. 2: Top view of the fabricated composite heater with five openings. The three openings at the center have a length of 10 μm and a width of 6 μm, while the two openings at the extremities have a length and width of 6 μm.
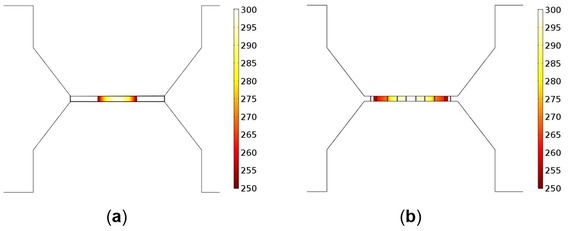
Fig. 3: Temperature distribution (°C) over the active area of (a) the initial design and (b) the novel composite heater design.