![]() |
|
||||
BiographyLuiz Felipe Aguinsky was born in 1990 in Porto Alegre, Brazil. He received his Bachelor's degree in Physics from the Federal University of Rio Grande do Sul (BSc, 2013). Subsequently, he studied Simulation Sciences at RWTH Aachen University (MSc, 2018), having written the Master's thesis at the German Aerospace Center. After finishing his studies he joined the Institute for Microelectronics in March 2018, where he is currently working on his doctoral degree. He is researching high performance numerical approaches for Technology CAD within the scope of the Christian Doppler Laboratory for High Performance TCAD. |
Monte Carlo Modeling of Low-Bias SF6 Plasma Etching of Silicon
Plasma etching of silicon using low-bias SF6 plasma is an important method in the microfabrication of microelectromechanical (MEMS) and semiconductor devices. The F radicals generated in the plasma can etch the silicon with high efficiency. Simultaneously, the low-bias reduces the kinetic energy of the ions accelerated towards the surface, thereby reducing the directional component of the etch. Consequently, this method usually generates surfaces with a high level of isotropy, similar to isotropic wet etching, while maintaining the advantages of gas-phase processing. In the manufacturing of large area optical devices, for example, dry etching techniques are favored since they generate cleaner surfaces.
The crucial challenge of modeling this process is capturing the exact characteristics of the isotropy. Three main approaches for such modeling are presented in Fig. 1. The straightforward approach, or strictly isotropic, is to assign the same velocity to all surface elements. Such an approach is illustrated in Fig. 1.a) and is the expected model for an ideal isotropic etch. However, experimental surfaces are known to not follow this exact shape, since it would generate a perfectly flat bottom. This indicates that there is etchant flux dependency, motivating the approach shown in Fig. 1.b). In this bottom-up approach, the velocities are weighted according to the hemispherical visibility of a defined source-plane, which serves as an approximation to the etchant particle flux.
A more general, physically richer model is illustrated in Fig. 1.c). This approach generates Monte Carlo particles in a source plane and tracks them through the simulation domain. A more physically motivated model is achieved by the introduction of a sticking probability, which then determines the reflection probability of the particle after interaction with a surface element. For each surface element, the velocity is weighted according to the contribution of all particles with it. This model effectively generalizes the two previous approaches, since the strictly isotropic model is recovered with a sticking probability near zero and the bottom-up with a sticking probability of unity.
We compare our approach to topography measurements of a fabricated surface. This cavity was generated with a two-step low-bias SF6 plasma etching process. The results are shown in Fig. 2, highlighting the modeling success of the top-down approach. The bottom-up approach is unable to capture the correct curvature due to its overemphasis of visibility dependence. While the strictly isotropic approach can qualitatively match the result, it clearly generates a perfectly flat bottom, which is incompatible with the reality of experimental devices. In conclusion, the introduction of the sticking probability as a modeling parameter allows the top-down approach to more accurately simulate low-bias SF6 plasma etching of silicon.
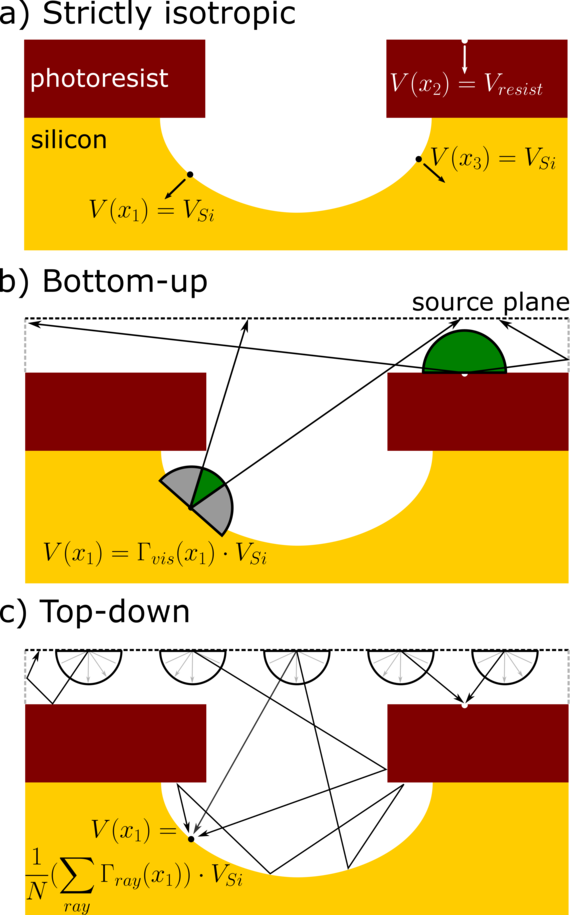
Fig. 1: Illustration of three approaches for modeling low-bias SF6 plasma etching. In a), it is assumed that all exposed surface elements of the same material propagate with the same velocity. The bottom-up approach in b) weights the velocity according to the hemispherical visibility of a source plane. For the top-down approach, shown in c), particles are generated and tracked through the simulation domain, contributing to the local velocity.
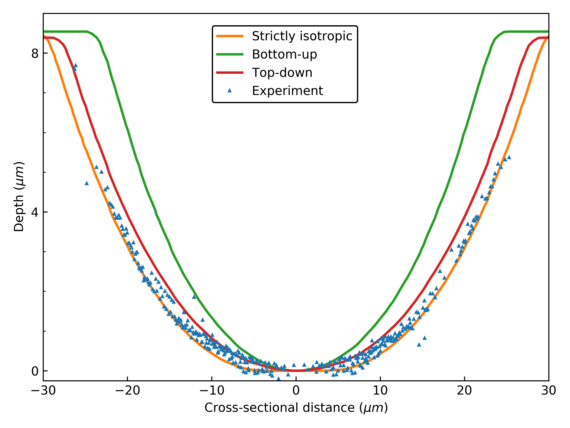
Fig. 2: Comparison of the modeling methodologies to an experimentally fabricated surface. The top-down approach can more accurately describe the surface, while avoiding artifacts such as the flat bottom seen in the strictly isotropic model.