![]() |
|
||||
BiographyXaver Klemenschits was born in Vienna in 1994. He studied Nanoscale Physics at the University of Birmingham, England, for which he received the degree of MSc in 2017. He joined the Institute for Microelectronics in August 2017, where he is working on topography simulation using different deposition and etching models. |
Geometric Surface Advection for Semiconductor Process Emulations
The modeling of semiconductor fabrication steps has become indispensable for the effective manufacturing of modern semiconductor devices. In order to model these processes efficiently and accurately, realistic descriptions of the involved materials and their interfaces are needed. However, such realistic simulations require a lot of computational power and time. It is therefore not feasible to simulate the entire fabrication process with all the intermediate steps. The simulation of important fabrication steps can offer valuable insight into critical process parameters, however, and how errors in one step affect subsequent processing steps. But in order to start simulations in the midst of the fabrication process, these intermediate structures still need to be created. They can either be drawn based on simple geometric parameters or created via process emulation, which uses the same geometric parameters and information from the processing steps, to automatically generate such intermediate structures.
In order to allow for the fast generation of such intermediate structures with high accuracy, a geometric advection scheme for the level-set method has been developed, which does not need to adhere to the usual restrictions of level-set advection. One such limitation is that the surface can only be moved half a grid spacing before it needs to be renormalized. Common advection schemes therefore need to be executed iteratively. In the proposed geometric advection scheme, the surface can be moved large distances at once, because the desired geometric distribution describing the movement is simply drawn on top of the old surface to create the advanced surface in a single step, as shown in Fig. 1. Furthermore, this approach does not introduce numerical errors, which can be propagated or even amplified in iterative approaches, resulting in an accurate representation of the advanced surface. The results for a simple trench structure for isotropic and directional growth are shown in Fig. 2 and Fig. 3. This approach can therefore be used to generate accurate structures quickly for subsequent physical simulations that rely on highly accurate initial geometries.

Fig. 1: The advanced surface is created by drawing the desired velocity distribution on the surface and taking its outline. As shown here, circles represent isotropic growth on the surface.
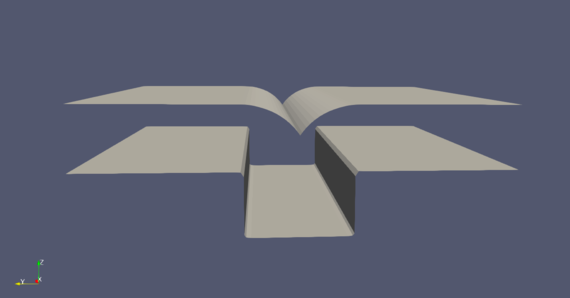
Fig. 2: Isotropic growth using the geometric advection scheme resulting in the expected new surface.

Fig. 3: Result of geometric advection of a trench using a velocity distribution for directional growth.