![]() |
|
||||
BiographyFrâncio Souza Berti Rodrigues was born in 1991 in Caxias do Sul, Brazil. He received his Bachelor's degree in Engineering Physics from the Federal University of Rio Grande do Sul (BSc, 2015). Subsequently, he received his Master's Degree in Microelectronics Manufacturing from the same university (MSc, 2018). After finishing his studies, he worked in research and development for the packaging industry before joining the Institute for Microelectronics in September 2019. He is currently pursuing his doctoral degree, researching high performance numerical approaches for Technology CAD within the scope of the Christian Doppler Laboratory for High Performance TCAD. |
Fluorocarbon Plasma Etching Modeling of Via Structures
Feature scale technology computer-aided design (TCAD) simulations of plasma etching processes are challenging due to the complexity involved and the great variety of physical and chemical mechanisms at play. With the continuous development of semiconductor devices, fabrication of structures with higher aspect ratios and higher density features is demanded from plasma etching technology. Fluorocarbon dry processes are particularly complicated because they exhibit simultaneous etching and deposition of protective polymer layers. The protective polymer layer prevents lateral etching and enables the fabrication of very high aspect ratio vias in DRAM and modern transistor technologies. The accurate modeling of fluorocarbon dry etching processes can thus greatly aid manufacturing developments driven by ever-growing performance demands.
We have implemented a modeling methodology for feature scale fluorocarbon Reactive Ion Etching (RIE) into Silvaco's process simulation tool Victory Process (Fig. 1). A bottom-up ray tracer is used to calculate the fluxes of chemical species into different geometries and source distributions. These fluxes serve as an input to a Langmuir set of coverage equations that describes the surface chemistry mechanisms. The coverage equations output the local etch or polymer deposition rates. A level-set engine applies the local rates to the whole surface and updates the geometry accordingly.
The complex plasma composition and its chemical reactions are abstracted to three different particle species: neutrals, polymers and ions. Neutral particles act as etchants, while polymers act as etch inhibitors that can also deposit protective layers. Ions are responsible for the RIE and physical sputtering etching mechanisms. Therefore, the Langmuir set of equations takes into account sputtering etching, chemical etching, RIE etching and polymer deposition mechanisms.
We applied the methodology to the via etching of SiO2 structures (Fig. 2). The polymer sidewall that inhibits lateral etching is essential for the fabrication of high aspect ratio structures. In addition, the faceting phenomenon present in the mask material is typical for materials for which the main etching mechanism is physical sputtering. To simulate these faceting structures and achieve accurate via shapes, we implemented different angular yield functions for RIE and physical sputtering mechanisms (Fig. 3). Our approach can be extended to different substrate materials and can be fully incorporated into TCAD workflows.

Fig. 1: Flow diagram of the methodology. The ray tracer evaluates the flux of neutral, polymer and ion particles. The Langmuir model outputs the etch or deposition rates, and the level-set engine updates the feature shape.
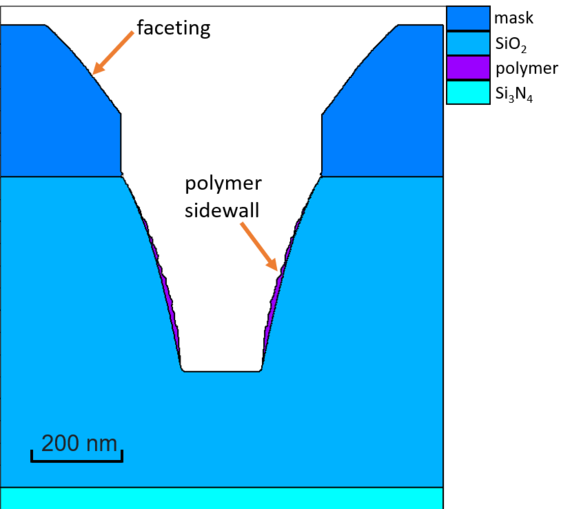
Fig. 2: SiO2 via etched for 25 s by an Ar/C4F8 fluorocarbon plasma. The polymer film protects the via sidewall and enables high aspect ratio features. Physical sputtering is the dominant etching mechanism for the mask material and that gives rise to the faceting phenomenon observed.
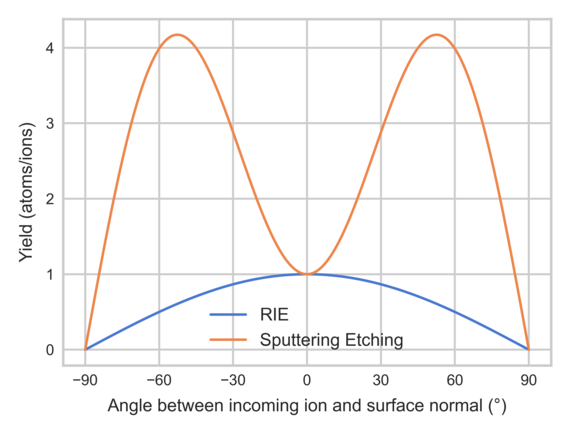
Fig. 3: Angular yield dependencies of RIE and sputtering etching mechanisms. The implementation of these angular dependencies is essential to simulate mask faceting and realistic via shapes.