Next: 7.2.2 Surface Advancement
Up: 7.2 Development
Previous: 7.2 Development
7.2.1 Development Rate Modeling
There exists a wide range of rate models ranging from purely empirical fits
to physical based approaches. We first describe the three most prominent
analytical models and then present well-established experimental results that
were obtained for the already mentioned IBM APEX-E resist
(cf. Table 7.1).
Dill's `E'-model. Along with the `ABC'-model describing the
exposure/bleaching phenomenon Frederick Dill also introduced a rate
model [74]. The dependence of the local development rate r(m) on the
normalized local PAC concentration m is thereby given by the
three-parameter equation
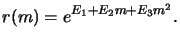 |
(7.18) |
The three parameters E1, E2, and E3 are obtained using
least-square fitting to experimental data. Experience shows that the
relationship (7.20) is capable of attaining good agreement
with data at high values of the inhibitor concentration m. However, it does
not properly characterize rates at low concentrations since it predicts
an unphysical rate maximum in this regime. This can usually be
ignored since the development rate for small m is so high that it can
be considered infinite anyway [74,208]. Dill's `E'-model was
the default model of early versions of the lithography simulator
SAMPLE [109]. Nowadays, it is often used because of its obvious
simplicity.
Kim's `R'-model. Deok Kim et al. addressed in [75]
the shortcomings of Dill's `E'-model. Two assumption were made to obtain
a more realistic expression to fit experimental rate data: Firstly,
the chemical reaction at the resist/developer interface is postulated to be
the rate-limiting process, which implies that the mass-transfer dynamics,
i.e., the diffusion process, can be neglected. Secondly, the time required
to dissolve a differential resist layer is assumed to consist of two
additive terms: (i) the time required to dissolve all the PAC in the layer,
and (ii) the time required to dissolve the photo-produced acid and all
other compounds. With these assumptions the resulting rate expression can be
written as
![$\displaystyle r(m)=\left[\dfrac{1-me^{-R_3(1-m)}}{R_1}+\dfrac{me^{-R_3(1-m)}}{R_2}\right]^{-1},$](img1143.gif) |
(7.19) |
whereby R1 is the dissolution rate of a fully exposed resist (m = 0),
R2 of an unexposed resist (m = 1), and R3 is a sensitivity parameter
with the interpretation of a rate enhancement due to photoinduced acid.
The first two parameters R1 and R2 can be measured, whereas the third
R3 has to be fitted. The proposed relation (7.21) contains
only three parameters. However, several additional R-parameters can be
included in an extended version to account for surface induction effects.
The depth dependent rate is then modeled by
 |
(7.20) |
The induction multiplier f (z, m) depends on the depth z into the
resist as well as on the PAC m. By choosing a decaying exponential
function for the vertical dependence like
an excellent agreement with measured data over the full exposure range
is obtained [75,209]. The parameters R5 and R6 describe
the ratio between surface and bulk rates for full and no exposure, respectively.
R4 is the characteristic retardation depth and is in principle only
determined by the resist and its processing. For certain resists the ratio of the
surface and bulk rate f (0, m) is a discontinuous function in the PAC m.
This can simply be accounted for by piecewise linear equations similar to that
proposed in (7.24) [75]. Kim's `R'-model is the
second rate model available in the lithography simulator SAMPLE [209].
Mack's `a'-model. Both so far described models provide mainly fitting
formulae with parameters having minor or no physical meaning. Chris Mack
proposed a four parameter model based on simple kinetic considerations with the
advantage that all involved parameters have physical
significance [107,210]. The approach relies on the assumption that
the development process involves two dominating mechanisms, namely the diffusion
of the developer from the bulk solution to the resist surface and the
reaction of the developer with the resist. Modeling the rates of both reactions
with fundamental kinetic theory and equating them yields
Here
rmin is the development rate of the unexposed resist, whereas
rmax is the rate of the fully exposed resist. The latter statement
is true provided that the experimental observation
rmin
rmax holds. n is a selectivity parameter that
describes the kinetic order of the dissolution reaction occurring at the
resist surface. The parameter
mth is a threshold PAC
concentration corresponding to the concentration at which the
development curve displays an inflection point. It can thus be interpreted as the
concentration of a transition between fast and slow development regimes.
The kinetic model (7.25) is based on the principle of
dissolution enhancement, i.e., it is assumed that the acid enhances the
dissolution of the resin/PAC mixture. In reality this is a simplification--there
is a second mechanism at work. The PAC acts to inhibit dissolution of the
resin while the acid acts to enhance the dissolution. An enhanced kinetic
model including both effects was proposed in [90] and takes the form
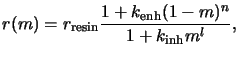 |
(7.25) |
where
kenh is the rate constant for the enhancement mechanism
of order n, and
kinh is the rate constant for the
inhibition mechanism of order l.
rresin stands for the
development of the resin alone. The enhanced Mack model is a superset of the
original `a'-model that neglects the inhibition phenomenon. Setting
kinh = 0 both Mack models (7.25)
and (7.27) are equal for the case that a is very large.
A large a implies a slow surface reaction in comparison to the mass transport
of the developer, i.e., the inflection point
mth is negative
(cf. (7.26)) meaning that the development process is only
governed by one process. This requirement for the comparison stems from the fact
that the enhanced Mack model does not account for the diffusion of the developer.
Finally, an empirical model like (7.24) can be used to describe
the positional dependence of the development rate. Both Mack models are
implemented in the PROLITH lithography simulator [108].
Experimental data for chemically amplified resists. The
dissolution rate of a positive deblocking chemically amplified resist
system is assumed to be a property of the deprotection level of the
polymer. This relationship can be determined from the measurements of
Nick Eib et al. for the IBM APEX-E resist [93].
The measured data show the dissolution rate versus exposure. Performing an
exposure simulation and applying the post-exposure bake model
of (7.16) the relation between rate and deprotection level
can be extracted. The thus obtained results are plotted in
Figure 7.2. A similar procedure is typically used for the
development simulation of other chemically amplified resists since the physical
processes are still not fully understood so that no physically meaningful model
has been provided until yet.
Figure 7.2:
Development rate of the IBM APEX-E chemically amplified resist as a function
of the normalized deprotection level x = 1 - m (after [93]).
|
Next: 7.2.2 Surface Advancement
Up: 7.2 Development
Previous: 7.2 Development
Heinrich Kirchauer, Institute for Microelectronics, TU Vienna
1998-04-17