Next: 6.5 Summary
Up: 6. Constrained Optimization of
Previous: 6.3 Evaluation and Optimization
6.4 Optimization Criteria and Results
Primarily two kinds of parameters could be optimized: speed
and energy efficiency.
But which definition of speed should be used, or does this
matter at all? And which criterion for energy efficiency
yields the best tradeoff between energy efficiency and speed?
Figures 6.6-6.15 show the resulting optimum
values as functions of the gate length. The curve parameter is the
optimization criterion. When the value plotted is present in the set
of optimization criteria the respective curve is plotted with a
thicker line.
For speed optimization five different criteria were used:
- 1.
- minimize
- 2.
- minimize
- 3.
- minimize
- 4.
- maximize
- 5.
- maximize

The traditional criteria are to maximize
or to minimize
on the
design side the available ``voltage drive''
(and thereby)
is kept a large as possible.
Despite the fact that an increase of
usually also improves
the performance it turns out that using the on-state current as an optimization
criterion does not yield optimal delay times, especially, when the
capacitive loading is small (
)
(Figs. 6.6 and 6.7).
The optima found with
and
as a criterion obviously
violate some criterion, so that the acceptable devices with maximum
lie closer to the ones with minimum
and
,
which may
be accidental (Figs. 6.8 and 6.9).
Minimizing the CV/I delay
metric
,
on the other hand, would foster about 50% larger real
delay times when the interconnect capacitance is larger (
).
The reason
is that minimizing
also minimizes the
gate capacitance per area, which decreases the available
(cf. Fig. 6.11).
Figure 6.6:
Optimal unloaded-inverter delay obtained by
unconstrained optimization with various delay criteria
|
Figure 6.7:
Optimal inverter delay obtained by
unconstrained optimization with various delay criteria
|
Figure 6.8:
Optimal unloaded-inverter delay obtained by
constrained optimization with various delay criteria
|
Figure 6.9:
Optimal inverter delay obtained by
constrained optimization with various delay criteria
|
Figure 6.10:
Optimal CV/I delay obtained by
constrained optimization with various delay criteria
|
Figure 6.11:
Optimal drive current obtained by constrained
optimization with various delay criteria
|
For the optimization of energy efficiency the following criteria were
applied to the data
- 1.
- minimize
- 2.
- minimize
- 3.
- minimize
- 4.
- minimize
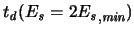
and the key results are shown in Figs. 6.12-6.15.
Taking just
as a criterion leads to very slow devices at only
a small improvement of the energy efficiency obtained by minimizing
.
For high-performance technologies the best way seems to be to minimize
the switching energy with a prescribed delay time, which is proportional to
the minimum
(Figs. 6.13 and 6.14).
At
the energy efficiency can still be improved
by a factor of 10 in comparison to the minimum-
case.
Furthermore, the devices can operate at much lower currents and
voltages (see Figs. 6.15 and 6.16)
Figure 6.12:
Optimal unloaded-inverter obtained by
constrained optimization with various energy criteria
|
Figure 6.13:
Optimal inverter delay obtained by
constrained optimization with various energy criteria
|
Figure 6.14:
Optimal switching energy obtained by
constrained optimization with various energy criteria
|
Figure 6.15:
Optimal drive current obtained by
constrained optimization with various energy criteria
|
Figure 6.16:
Optimal supply voltage obtained by
constrained optimization with various energy criteria
|
Figure 6.17:
Optimal linear threshold voltage obtained by
constrained optimization with various energy criteria
|
Next: 6.5 Summary
Up: 6. Constrained Optimization of
Previous: 6.3 Evaluation and Optimization
G. Schrom