Next: 3.3 Model Overview
Up: 3. Advanced Oxidation Model
Previous: 3.1 The Diffuse Interface
Subsections
From the mathematical point of view the whole oxidation process can be described by a coupled system of partial differential equations, one for the diffusion of oxidants through SiO
, the second for the conversion of Si into SiO
at the interface, and a third for the mechanical problem of the complete oxidized structure.
3.2.1 Oxidant Diffusion
The diffusion of oxidants in the domains
,
, and
according to Fig. 3.1 is described by
 |
(3.2) |
where
is the Laplace operator,
is the oxidant concentration in the material, and
is the temperature dependent low stress diffusion coefficient.
The boundary conditions for the diffusion equation (3.2) are
 |
(3.3) |
where
is the oxidant concentration in the gas atmosphere.
is a Neumann boundary condition, which means that there does not exist an oxidant flow through these boundaries.
In (3.2)
is the strength of a spatial sink and not just a reaction coefficient at a sharp interface [67].
defines how many particles of oxygen per unit volume are transformed in a unit time interval to oxide.
is defined to be linearly proportional to
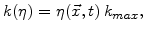 |
(3.4) |
where
is the maximal possible strength of the sink.
Figure 3.1:
Schematic domains and boundaries.
|
3.2.2 Dynamics of
Because of the chemical reaction which consumes silicon, the normalized silicon concentration
is changed. In a test volume
, where is assumed that the oxidant concentration C is constant during a time interval 
there are
particles of oxygen which react with
unit volumes of silicon. By this process the silicon concentration is reduced.
The dynamics of
can be described by [67]
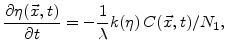 |
(3.5) |
where
is the volume expansion factor (=2.25) for the reaction from Si
to SiO
, and
is the number of oxidant molecules incorporated into
one unit volume of SiO
.
In this model the dynamics of
is equivalent with the movement of the sharp Si/SiO
interface in the standard model, because
defines the silicon and oxide areas. The only difference is that here a diffuse interface (Fig. 3.1) moves, where is a mixture of silicon and oxide.
3.2.3 Volume Expansion of the New Oxide
Because of the much lower density of oxide compared with silicon, the conversion from Si to SiO
leads to a significant volume increase of the new oxide.
In the advanced model the conversion is not performed instantaneously, it needs some finite time. The fraction of SiO
in a small volume
is expressed by the
value. The new generated oxide in the reaction layer is described by the change of
. For a time period
the
-value and the silicon fraction decreases with
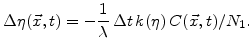 |
(3.6) |
The additional volume in a test volume
is given by
 |
(3.7) |
Because the maximal volume increase of the oxide is limited to 1.25 times of the volume of original silicon,
in (3.7) must be scaled with (
).
The normalized additional volume with (3.6) and (3.7) after a time
is
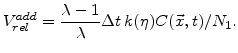 |
(3.8) |
An important aspect of (3.8) is that the sum of
over all time steps can not be more than 125%, which is the maximal volume increase of the material during oxidation.
3.2.4 Diffusion Coefficient and Reaction Layer
In contrast to the standard models, where the diffusion coefficient
is automatically included in the parabolic rate constant B, in the advanced model
must be determined separately for the specific temperature and oxidant species. The most interesting oxidant species come from dry and wet oxidation.
In general the diffusion coefficient follows the expression
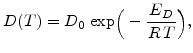 |
(3.9) |
where
is a pre-exponential diffusion constant,
is the activation energy in [cal], T the temperature in [K], and
is the universal gas constant with
cal/(K
mol).
For dry oxygen ambients the results of Norton [68] can be used, who found that the activation energy for diffusion of oxygen in vitreous silica is 27 kcal and the diffusion coefficient
is 4.2
cm
/sec (= 0.42
m
/sec) at a temperature of 950
C. With these data it is possible to calculate
, and (3.9) can be written for dry oxidation in the form
 |
(3.10) |
For wet oxidation the results from Moulson and Roberts [69] are most suitable. They have investigated heated silica glass in water vapour between 600 and 1200
C and found the temperature dependent diffusion coefficient
 |
(3.11) |
In the advanced model the reaction layer has a spatial finite width d
, which can vary. This width is mainly determined by the value of
. The bigger
, the steeper the concentration decay and the thinner the reaction layer.
Therefore, d
is inverse proportional to
and so the width can be controlled by
. This means that a small value of
(e.g.
) leads to a wide reaction layer (e.g d
nm) and a big value of
(e.g.
) leads to a small reaction layer (e.g d
nm).
The layer width is an important and necessary fact, because the thickness of the reaction layer must be much smaller than the thickness of the oxidized structure or the final oxide thickness. In order to apply this model also for dry or thin film oxidation with a few nm thickness, wide reaction layers are unusable.
Another interesting aspect of this model is the value of the diffusion coefficient
in the reaction layer. In the standard model with a sharp interface the oxidants diffuse with the same
through the oxide to the Si/SiO
-interface where they react. This means that in the standard model no oxidants diffuse into silicon and a normalized coefficient
in the silicon and
in the oxide are appropriate.
In the advanced model the oxidant diffusion must not stop at the beginning of the reaction layer, because there the oxidants are needed for the chemical reaction. On the other side the oxidant diffusion should stop at the end of the reaction layer and not continue into the silicon material. A good approach for this model is that the values of
run down gradually from an approximate value of 1 near the oxide area to a value of 0 near the silicon area as schematically shown in Fig. 3.2.
Since
defines the domains of oxide, reaction layer as well as silicon, and during the oxidation process the reaction layer moves into the silicon domain,
must be a function of
. Because the value of
must be 1 in SiO
, where
, and 0 in Si, where
(see Fig. 3.2), the most plausible function for the diffusion coefficient in the reaction layer is
 |
(3.12) |
Another simple but good working formulation for
in the reaction layer was found with
 |
(3.13) |
Here
is a small constant and
must be limited to
when
.
Figure 3.2:
Values of
and D
in the reaction layer.
|
3.2.5 Mechanics
The chemical reaction of silicon and oxygen causes a volume increase of about 125%, which leads to significant displacements in the material. If this volume increase is only partially prevented, mechanical stress is built up in the materials. In order to calculate these displacements and stresses a mechanical modeling is needed.
In general, every three-dimensional mechanical problem can be described by the stress equilibrium relations [70]
During the oxidation process there are normally no external forces, because a volume increase caused by a chemical reaction, or a thermal expansion only lead to internal forces. Therefore, on the right-hand side of (3.14) the external forces are
.
For linear elastic materials which are described by the Hook's law, the stress tensor
from (3.14) is given by
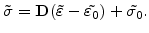 |
(3.15) |
Here
is the so-called material matrix. Furthermore,
is the strain tensor,
is the residual strain tensor, and
is the residual stress tensor.
For constructing the material matrix
, the components of the stress tensor without residual stress and strain components can be expressed in Lame's form by [71]
 |
(3.16) |
where
is the trace of the strain tensor
 |
(3.17) |
is the Kronecker symbol
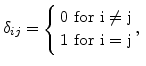 |
(3.18) |
and
and
are the so-called Lame's constants
 |
(3.19) |
Thereby
is the Young modulus and
is the Poisson ratio. Note, the often used shear modulus
is identical with Lame's constant
.
The strain tensor is
![$\displaystyle \tilde{\varepsilon}= \left[ \begin{array}{ccc} \varepsilon_{xx} &...
...\gamma_{zx} & \frac{1}{2}\gamma_{zy} & \varepsilon_{zz} \end{array} \right].$](img301.png) |
(3.20) |
The elements
are the first derivatives of the displacements
so that
 |
(3.21) |
The shear strain components
are given by [72]
 |
(3.22) |
If an isotropic material is assumed, the strain tensor is symmetric due to
 |
(3.23) |
which means that there are only six different values.
Assuming an isotropic material and after constructing
with the help of (3.16), the stress tensor without residual stress, can be rewritten in the form
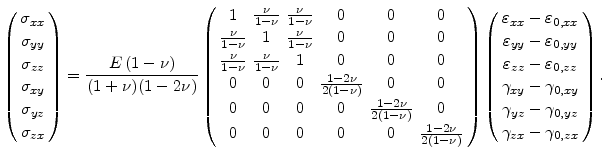 |
(3.24) |
3.2.5.2 Visco-Elastic Mechanical Model
The material behavior of oxide and nitride are more realistically described with a visco-elastic model [73,74], especially with a so-called Maxwell element (see Fig. 3.3), which consists of a spring and a dashpot in series. The characteristics of such a Maxwell element is that it takes the stress relaxation and the stress history into account. Also the actual stress is influenced from both, the strain and the strain rate, and, therefore, the stress is a function of time. The Maxwell element can be mathematically formulated with
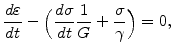 |
(3.25) |
where
is the shear modulus and
is the (shear) viscosity.
Figure 3.3:
Maxwell element: a spring and a dashpot in series.
|
The analytical solution of (3.25) for the temporal stress evolution as a function of the strain velocity is
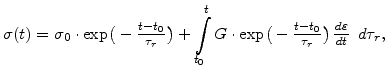 |
(3.26) |
where
is the initial stress at time
and
is the Maxwellian relaxation time constant
 |
(3.27) |
In (3.26) the first term shows that the initial stress relaxes exponentially with time. The evaluation of the integral part leads to
 |
(3.28) |
The visco-elastic model is based on the idea that the dilatational components of the stress, which involve the volumetric expansion or compression, and the deviatoric components which only include the shape modification, can be decoupled [75]. For this purpose the material matrix
from (3.24) can be split in a dilatation and a deviatoric part [76]
![$\displaystyle \mathbf{D}=\mathbf{D}_{dil}+\mathbf{D}_{dev}= \left(H\left[ \begi...
...om{-}0 &\phantom{-}0 &\phantom{-}0 &\phantom{-}1 \end{array} \right] \right).$](img318.png) |
(3.29) |
Here
is the bulk modulus
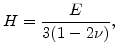 |
(3.30) |
and
is the so-called effective shear modulus which is in the elastic case the same as the standard shear modulus
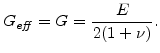 |
(3.31) |
In Maxwell's model the dilatation part is assumed purely elastic, while the deviatoric part is modeled by the Maxwell element.
In order to find an uncomplicated Maxwell formulation for the deviatoric part in (3.29), it can be assumed in (3.28) that for a short time period
the strain velocity can be kept constant
 |
(3.32) |
so that (3.28) can be expressed in the form
 |
(3.33) |
So in the visco-elastic case
can be written in the form [77,78]
 |
(3.34) |
This relationship shows that the Maxwell visco-elasticity can be expressed by an effective shear modulus
in the deviatoric part of the material matrix
(3.24). This means that the only difference in the mechanical model between the elastic and visco-elastic case is the different
in the material matrix
. So
depends in the elastic case only on Young's modulus
and the Poisson ratio
, and in the visco-elastic case additionally on the Maxwellian relaxation time
.
A very important aspect in the oxidation model is, how the volume increase during oxidation can be brought in relation with the mechanical problem. In three dimensions a volume expansion can be formulated with
 |
(3.35) |
where
is the normalized volume before expansion and thus
is always 1.
By assuming that the volume expansion and the strain is small, the strain terms
can be neglected (
and
stands for
,
or
), because they are much smaller than the terms
. Therefore, with the start volume
, (3.35) can be reduced to the form
 |
(3.36) |
The components
of the residual strain tensor
are linearly proportional to the normalized additional volume as calculated in (3.8)
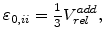 |
(3.37) |
which loads the mechanical problem (3.15) for calculating the displacements and stresses.
Next: 3.3 Model Overview
Up: 3. Advanced Oxidation Model
Previous: 3.1 The Diffuse Interface
Ch. Hollauer: Modeling of Thermal Oxidation and Stress Effects